Going with the Flow
From Taiwanese semiconductor shortages, to stuck ships plugging the Suez Canal, to mysteriously missing boxes of bran flakes on grocery shelves, the global supply chain has finally come to the foreground, where it belongs. As part of this pandemic era reckoning, a May 2021 CLUI research project explored the landscape of Amazon’s logistics in Southern California (where as of this writing, dozens of container ships still loiter off the port, waiting to drop their loads).
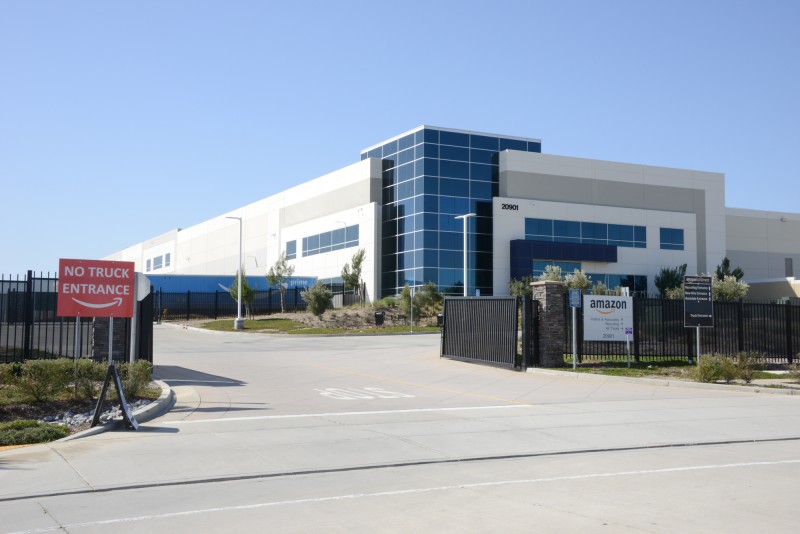
AMAZON’S RETAIL DISTRIBUTION NETWORK, expanding in a wave across the nation over the past decade, and fueled dramatically over the past year of the pandemic, is especially evident in the greater Los Angeles region, a place some call the Southland. Amazon has at least 28 large logistics warehouses and fulfillment centers in the area. The first of these facilities opened ten years ago, and ten of them have opened over the last few years. The facilities serve a population of more than 20 million people, and are fed by the largest port in the nation, as well as one of the largest warehousing and logistics regions in the nation, the Inland Empire—where all but two of Amazon’s fulfillment and logistics centers in the Southland are located.
From the outside the structures have a similar appearance: they are typical large logistics warehouses with loading docks, ranging in size from 300,000 to 1,200,000 square feet, and are generally windowless except perhaps in the lobby and administration area in the front of the building. They are usually surrounded by other, similar-looking buildings, in office parks in logistically favorable locations, near highway junctions.
Activities and machinery inside vary according to the functions of the facility, such as inbound inventory sorting and warehousing, fulfilling orders for goods of varying size, organizing outbound packages by destination, or other forms of warehousing. Amazon has three types of facilities: receive centers, sortation centers, and fulfillment centers, which are the most common, and which fall into two types: sortable and non-sortable.
Fulfillment centers are where orders are filled, by pulling items off shelves and putting them in boxes for shipment to customers. Small sortable fulfillment centers are for items measuring less than 18 inches, and weighing up to around 25 pounds. Items bigger than this, but still small enough to fit in boxes, and placed on shelves and conveyors, are handled in large sortable fulfillment centers. Items weighing more than 60 pounds, or especially large or bulky items, like furniture and carpets, are handled by non-sortable fulfillment centers.
There are six small sortable fulfillment centers in the Southland. They are typically around 800,000 square feet, and employ around 1,500 people. Human operations generally fall into three categories: pickers, who pick items off shelves and put them into totes and carts; packers, who pack boxes for shipment and put them on conveyor belts; and stockers, who replenish the shelves. As with other types of fulfillment centers, operations are either inbound or outbound.
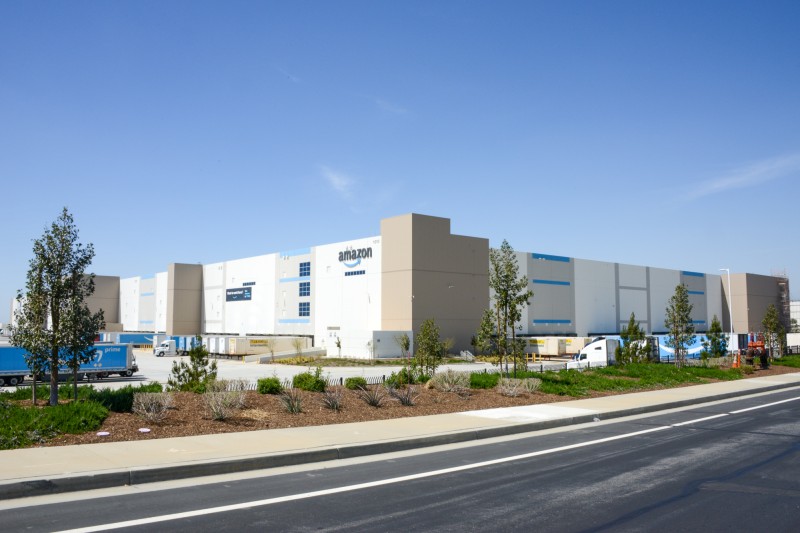
Inbound
Inbound starts at the receive dock, where semi-trucks bring inventory from wholesalers, Amazon receive centers, or vendors using “Fulfilled by Amazon” services (which constitute half of the orders processed by Amazon). Items enter the inbound receive line, where they are checked in, verified by hand, barcode scanned, and precisely weighed. The items then head to the shelves, where they are stored using Amazon’s randomized stow method. Though perhaps counterintuitive, the company has found that maintaining an arbitrary storage system, instead of an organized one, makes for a more efficient stowing and picking process, with less time spent moving the inventory around, limiting bottlenecks, and increasing the likelihood that the item is closer to where it needs to be for the fulfillment process. Items are placed on the nearest empty space on the nearest shelf. Each shelf has a barcode, with its location information. As the item is placed on the shelf, it is scanned (again) with a hand scanner, along with the code for the shelf it is stowed on, linking the two so that the item can be found when the time comes for it to go outbound. The 14 million items in a standard 850,000-square-foot fulfillment center may be stored randomly, physically, but each item’s identity and location is precisely organized electronically.
Traditional fulfillment centers, built before robotics were brought in over the last few years, have fixed shelving divided into storage rack areas called mods. Human stowers and pickers take carts and totes to the mods to stow items or retrieve ordered items. Robotic small sortable fulfillment centers, built over the past few years, bring the shelves to the stowers and pickers, employing movable towers of shelves called pods. The pods are elevated by wheeled robotic drive units, which scoot underneath the pods, lifting them a few inches off the floor, to shuttle them where they need to go. These robotic floors are off-limits to humans, and are gridded out with QR codes, which guide the robots, moving hundreds of shelves around at five feet per second, in an elaborate algorithmic dance of replenishment and fulfillment.
Outbound
In a traditional fulfillment center, outbound begins when a picker heads out to the mods with a tote. In a robotic fulfillment center, robots bring the shelving pods to the picker. Either way, scanned plastic tote boxes are filled with scanned items, and placed on a conveyor. Fulfillment centers can have up to 20 miles of conveyors moving totes and boxes around. Orders in totes go to a pack station, where human packers place the items in boxes, along with dunnage (paper or plastic air pillows) to fill the voids. Once the box is sealed, it gets a spool label (SPL), with a barcode linked to the order and customer information, used for identifying the box when it goes back on a conveyor to the next step in the process, the SLAM.
SLAM (scan, label, apply, manifest) occurs as the box moves along a conveyor belt. When the box is scanned, the dimensions of the box are automatically measured, the box is weighed to confirm contents, and the spool label is read to indicate the contents and to generate a customer address for the shipping label. A few feet further down the conveyor, the label is generated, printed, and applied by a machine, with a manifest printed in barcode and letter code, which says where the box goes next based on time, demand, and destination.
The conveyor belt takes the box to the last step, the ship sorter, where a conveyor with shunting shoes along its length kicks the box onto the designated ramp, leading to a loading area where a truck going to the right place is either waiting, or soon to be arriving at the outbound shipping docks.
Non-sortable fulfillment centers handle items too large or bulky to be automated, like exercise equipment, patio furniture, and large televisions. These buildings function more like regular warehouses, with tall fixed shelving, forklifts, and few robots or conveyor belts. The buildings range in size from 600,000 to 1,000,000 square feet. There are seven or so of these facilities in the Southland.
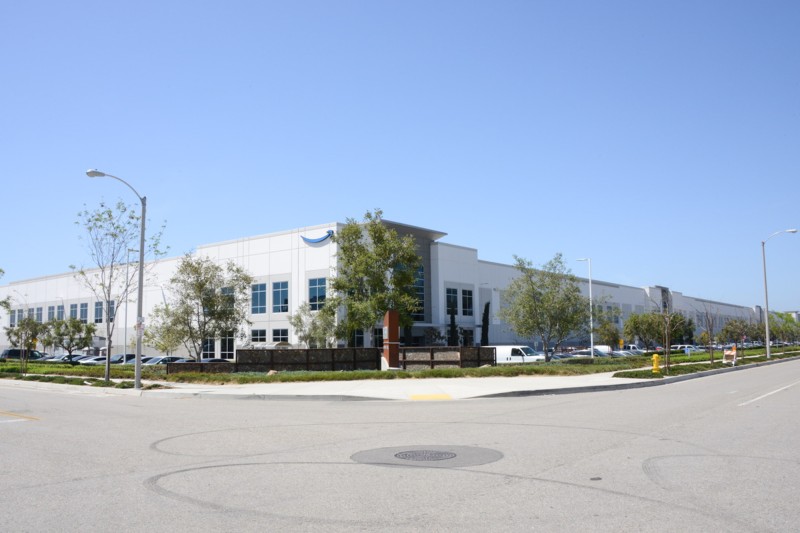
Beyond Fulfillment
Receive centers are where some high-volume inbound inventory is sorted and stored before going to fulfillment centers. Inside, goods arriving from suppliers are offloaded, sorted, and either stored or quickly sent to Amazon’s fulfillment centers. There are currently a couple of dozen Amazon receive centers in the USA, located near ports and major urban areas. Six of these are in the Southland (a high proportion since it has the nation’s largest port, and is the main gateway for products coming from China). Receive Centers are typically around 600,000 square feet in size.
Sortation centers are another type of Amazon facility, on the outbound side of operations. They aggregate outbound packages from the region’s fulfillment centers, and sort them according to destination and carrier method. Inside sortation centers, packages are palletized and grouped by zip code for shipment to local Amazon Delivery Stations, other delivery companies (like FedEx), the US Postal Service, or those destined for air hubs. Presorting in this way can shave a day or more off of shipping time, facilitating two-day nationwide delivery. It keeps more packages inside Amazon’s own delivery network, reducing the need for other shipping companies, with their inherent delays and costs.
There are currently several dozen outbound sortation centers in the nation, with some located inside fulfillment centers. There are four Amazon buildings dominated by this function in the Southland, ranging in size from 200,000 to 600,000 square feet.
Amazon has a category for specialty operations, in warehouses that focus on specific types of products, like shoes, or products with demand that surges periodically, like Halloween costumes, and these buildings often can accommodate extra employees and operations during the holiday shopping season. There are a few of these buildings around the Southland, near other Amazon fulfillment facilities.
Amazon operates two air terminals in the Southland too, both at commercialized military bases, and many of the fulfillment centers, sort centers, receive centers, and specialty buildings are clustered around these airports. One of them is March Field, a former Air Force Base in the southern part of the Inland Empire. Known as Amazon’s Inland Empire Air Hub, the terminal is a 70,000-square-foot warehouse building on the flightline, with a busy truck yard, and parking spaces for lines of aircraft. Though Amazon uses other airports in the Southland, and also uses other air cargo companies to carry its shipments, at the moment this is the company’s principal air cargo port in the Southland.
Amazon currently has around 75 Prime Air cargo planes which are now being routed to ferry goods between one of 25 gateway airports like this to its new $1.5 billion, three-million-square-foot sorting hub in Kentucky, across the Ohio River from Cincinnati. Amazon boxes and goods not destined for local delivery arrive at March Field, sorted by destination zip codes from the Southland’s fulfillment centers by the end of the day. Packages are flown to the Kentucky air hub at night, where they are sorted and loaded onto planes that then take them to their destination air gateway airport, wherever that may be. The same planes then bring packages bound for Southland destinations back to March Field. In the past Amazon has mostly used FedEx and UPS for air shipments, but now, with its own aircraft and hub and spoke air cargo facilities coming online, it is becoming a major air cargo operation itself.
There are a few Amazon fulfillment centers around March Field, but the largest cluster in the Southland is around San Bernardino International Airport. The airport operated for decades as Norton Air Force Base, until it closed in 1994. It is now mostly a cargo airport used by FedEx, UPS, Amazon, and other freight carriers. The first Amazon fulfillment center in the Southland, ONT2, opened here in 2012, and there are more than a half dozen Amazon facilities in the office parks that have developed on the periphery of the airport, including a receive center and sortation center.
The second of Amazon’s dedicated airport facilities in the Southland opened here in 2021. Known as the East Gate Air Cargo Logistics Center, the facility has a main building around 660,000 square feet, and two smaller buildings. 15 or so Amazon Prime Air cargo planes are based there, with around 25 take-offs and landings expected to take place daily.
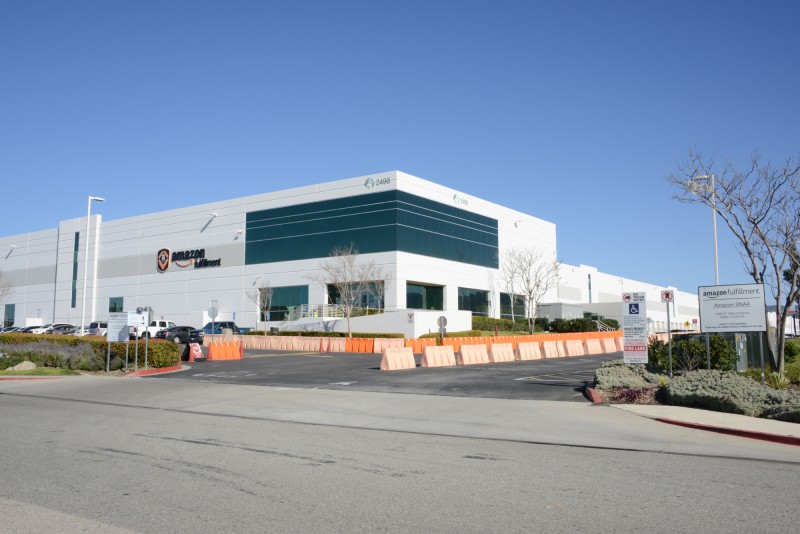
Amazon Delivery: The Last Mile
Beyond the fulfillment logistics operations based out of the Inland Empire is Amazon’s even more rapidly expanding local delivery hub network, serving the last-mile delivery needs for the Southland’s 20 million residents. This network is located inside the urban areas where most of the population lives, especially in the LA basin.
The main facility type is a delivery station, where packages arrive from outbound sortation and fulfillment centers, and are further sorted into specific regions for final delivery to customers, by van, and by Amazon Flex gig workers in their own vehicles. Many of the vans are leased from Amazon by delivery service partners, independent small companies licensed and trained by Amazon to deliver for them, using Amazon vehicles and uniforms.
Amazon started its delivery service in 2013, aiming to reduce its dependence on UPS and other delivery companies (as well as the US Postal Service, which Amazon used a great deal, and hired to make Sunday deliveries, starting in late 2013). The first group of delivery facilities were small pre-existing warehouse buildings, generally 50,000 square feet in size or less. Today the majority of delivery facilities are around 150,000 square feet, though some are more than 300,000 square feet.
While the main function is loading vans (either outdoors or indoors), some delivery stations are open for customer pickups and returns. A few of the facilities are dedicated to large and bulky items, which generally use bigger delivery trucks with hydraulic tailgates, and offer white-glove service. There are currently around 35 delivery stations in the Southland, half of which opened in the last two years. Nationally there are more than 400 delivery stations, and the company is building hundreds more. Two years ago, there were less than 200. ♦
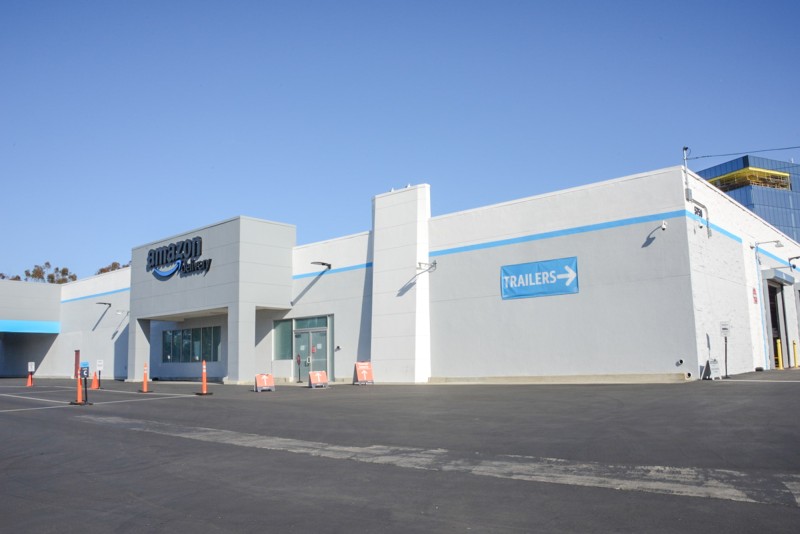
Reading the Box
Packages from Amazon show their provenance on their labels:
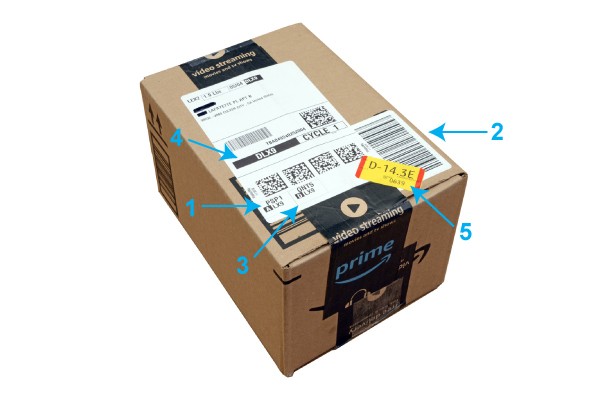
1. PSP1
The order in this package was filled at PSP1, a small sortable fulfillment center in Beaumont. The names of most Amazon distribution facilities contain three letters, followed by a number. For the most part, the letters are international airport codes. Sometimes these airports have a direct connection to the facility, by proximity or as a gateway airport used for shipping, but this is not always the case. PSP is the code for Palm Springs International Airport.
2. Spool Label Barcode
SPL or spool labels are generated at fulfillment centers, and are the first label applied to the box, as soon as it is sealed with the order inside. The barcode links to a computer ID that has the customer’s name and address, and order information. The label is only used internally by the fulfillment center, and is scanned along the SLAM (scan, label, apply, manifest) line, which generates the bigger shipping and manifest label, the main label on the box.
3. ONT5
This package then went to ONT5, one of four Amazon outbound sortation centers, which collect and organize outgoing packages to get them to their final destination more efficiently. ONT5 references Ontario International Airport (ONT), though it is located next to San Bernardino Airport (SBD). Other airports in the Southland that are part of Amazon facility names include SNA (John Wayne Airport), Chino Airport (CNO), March Field (RIV), and Los Angeles International Airport (LAX).
4. DLX9
The next stop for this package was DLX9, a delivery station near Jefferson Boulevard, that serves the Culver City region. Delivery station names generally begin with a D, followed by a regional code, such as LA for Los Angeles, though usually less literal, such as this one, DLX9. From here the package was placed in a delivery truck, and dropped on the customer’s doorstep in Culver City.
5. Delivery Station Label
The yellow label is applied at the delivery station, providing delivery area and sequence numbering to help sort the packages being loaded onto the local delivery trucks or in the private vehicles of Amazon Flex gig workers.